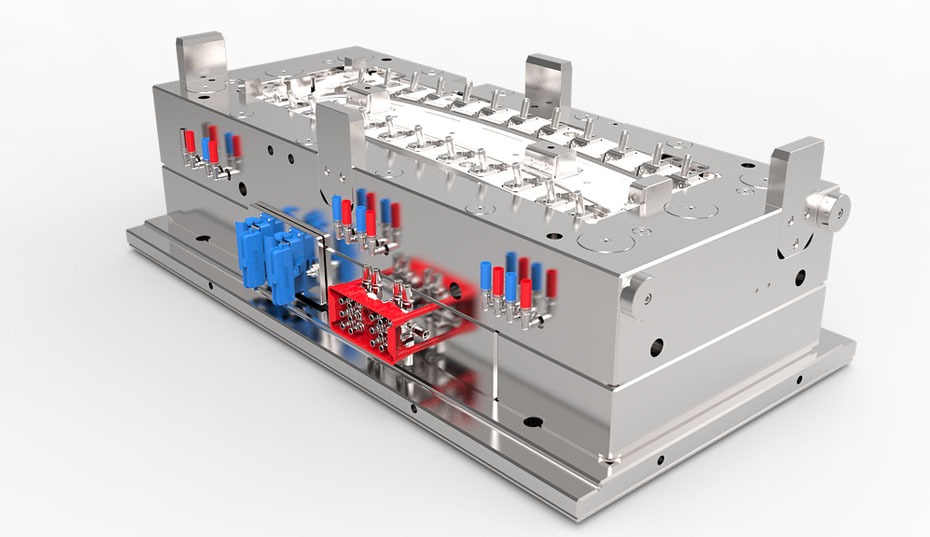
Injection molding is a manufacturing process for creating parts by injecting material into a mold. It is commonly used for plastics, but can also be used for metals and other materials. Injection molding machines heat the material, typically plastic, and inject it into a mold where it cools and solidifies into the desired shape. The process is highly efficient and can produce large numbers of parts quickly and with a high degree of accuracy.
Injection moulding is an incredibly efficient and cost-effective way to produce parts in large quantities. From automotive components to medical devices, injection moulding is used to make a wide variety of products and is a key technology in the manufacturing industry. In this article, I’m going to break down the basics of what injection moulding is, the benefits it provides, and how it works. So, let’s get into it!
Introduction to Injection Moulding
Injection moulding is a manufacturing process used to mass-produce plastic parts. It involves heating a plastic raw material and injecting it into a mould cavity. The mould cavity is then cooled and the part is ejected. Injection moulding is a reliable and repeatable manufacturing process, capable of producing high-quality, complex parts with tight tolerances.
Injection moulding is one of the most popular manufacturing processes in the world, and is used to produce a wide variety of products. From medical devices and consumer electronics to automotive components and industrial parts, injection moulding is used for a wide range of applications.
What is injection moulding?
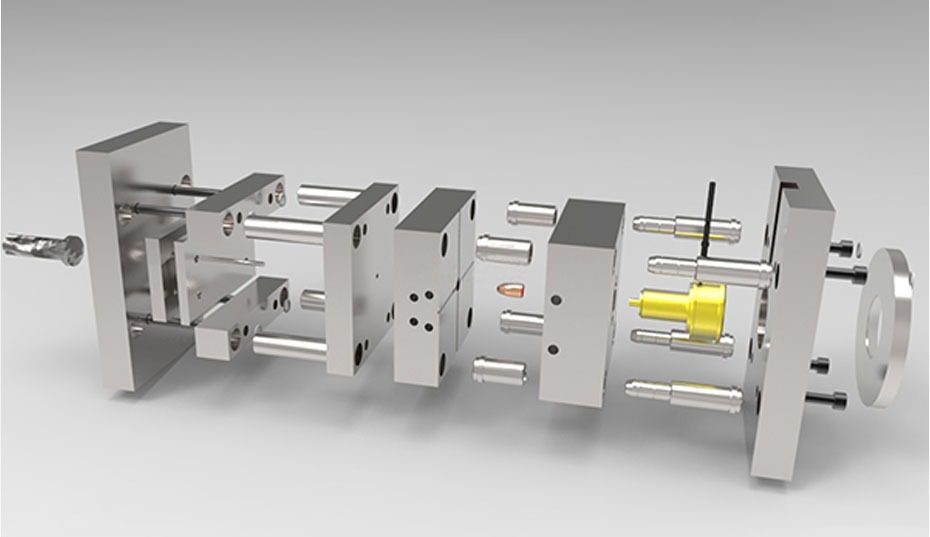
Injection moulding is a manufacturing process used to produce plastic parts. It involves melting a plastic material, usually a thermoplastic, and injecting it into a mould cavity. The mould cavity is cooled and the part is ejected. The process is fast, repeatable and capable of producing complex parts with tight tolerances.
Injection moulding is an incredibly efficient process, capable of producing large volumes of parts in a single run. It’s also one of the most cost-effective methods of mass-producing plastic parts. Injection moulding is used to produce a wide variety of products, from medical devices and consumer electronics to automotive components and industrial parts.
Benefits of injection moulding
Injection moulding is an incredibly efficient and cost-effective way to mass-produce parts. Here are some of the key benefits of the process:
- Speed: Injection moulding is a fast process, capable of producing large volumes of parts in a single run.
- Cost-effectiveness: Injection moulding is one of the most cost-effective methods of mass-producing plastic parts.
- Reliability: Injection moulding is a reliable and repeatable process, capable of producing high-quality, complex parts with tight tolerances.
- Versatility: Injection moulding is used to produce a wide variety of products, from medical devices and consumer electronics to automotive components and industrial parts.
- Automation: Injection moulding machines can be automated, allowing for more efficient production.
- Design flexibility: Injection moulding offers greater design flexibility than other manufacturing processes, allowing for more complex parts to be produced.
Steps in the injection moulding process
Injection moulding is a complex process, but it can be broken down into four key steps:
- Clamping: The first step in the injection moulding process is clamping. The mould is clamped shut, which prevents the molten material from leaking out.
- Injection: The molten material is then injected into the mould cavity. The material is injected at high pressure and the mould is filled in a matter of seconds.
- Cooling: The mould is then cooled, which allows the material to solidify and take the shape of the mould cavity.
- Ejection: The part is then ejected from the mould.
Injection moulding materials
Injection moulding is used to produce a wide variety of parts, using a variety of materials. The most common materials used in injection moulding are thermoplastics, such as polyethylene, polypropylene and ABS. Other materials, such as elastomers and thermosets, can also be used.
The material used for injection moulding will depend on the application and properties required. Different materials have different properties, such as strength, flexibility and resistance to heat and chemicals. Choosing the right material for the application is critical to ensure the part performs as expected.
Common applications of injection moulding
Injection moulding is used to produce a wide variety of products, from medical devices and consumer electronics to automotive components and industrial parts. Here are some of the most common applications of injection moulding:
- Automotive: Injection moulding is used to produce a wide range of automotive components, including bumpers, interior trim, door panels, dashboards and more.
- Electronics: Injection moulding is used to produce a wide range of electronic components, such as connectors, switches, circuit boards and more.
- Medical: Injection moulding is used to produce a wide range of medical devices, such as syringes, catheters and other medical products.
- Packaging: Injection moulding is used to produce a wide range of packaging products, such as bottles, containers and lids.
- Industrial: Injection moulding is used to produce a wide range of industrial parts, such as valves, fittings and other components.
Injection moulding machines
Injection moulding machines are the backbone of the injection moulding process. The machines are designed to melt the plastic material and inject it into the mould cavity. Injection moulding machines are available in a range of sizes and configurations, depending on the application.
Injection moulding machines are highly automated, allowing for greater efficiency and repeatability. They can be programmed to automatically adjust the temperature, pressure and other variables to ensure the part is produced to the highest quality and accuracy.
Injection moulding services
Injection moulding services are available to help you design and produce parts using the injection moulding process. Injection moulding services can help you design your part, develop the mould and produce the parts. They can also provide additional services, such as post-processing, assembly and packaging.
Injection moulding services can provide a range of support to ensure your parts are produced to the highest quality and accuracy. They can help you choose the right material, optimise the mould design and streamline the production process.
Injection moulding design tips
When designing parts for injection moulding, it’s important to consider the process and the material being used. Here are some tips to help you design parts for injection moulding:
- Consider the shrinkage rate: Different materials have different shrinkage rates, so it’s important to consider this when designing the part.
- Consider the draft angle: The draft angle of the part should be considered to ensure the part can be easily ejected from the mould.
- Consider the wall thickness: The wall thickness of the part should be considered to ensure the part is strong enough to withstand the injection moulding process.
- Keep it simple: It’s important to keep the design as simple as possible to reduce manufacturing costs.
- Consider the mould design: The mould design should be considered to ensure the part is produced with the highest quality and accuracy.
Injection Moulding FAQ
- What is injection moulding? Injection moulding is a manufacturing process in which molten material, typically plastic, is injected into a mould and solidifies to form a specific shape.
- What are the most common materials used in injection moulding? The most common materials used in injection moulding are thermoplastics, such as polyethylene, polypropylene, polystyrene, and ABS.
- What are the advantages of injection moulding? Injection moulding has several advantages, such as high production rates, low labor costs, and the ability to produce complex, detailed parts with tight tolerances. Additionally, it is a versatile process that can be used to produce a wide range of products, from simple household items to complex automotive parts.
- What are the limitations of injection moulding? Injection moulding has some limitations, such as high initial costs for tooling and moulds, and a limitation on the size and weight of the parts that can be produced. Additionally, certain materials, such as elastomers and thermosetting plastics, cannot be processed using injection moulding.
- How long does it take to create a mould for injection moulding? The time it takes to create a mould for injection moulding can vary depending on the complexity of the design and the number of cavities required. It typically takes several weeks to several months to design, fabricate and test the mold.
- How is the quality of the finished product ensured in injection moulding? Quality assurance in injection moulding is achieved through the use of detailed specifications, careful design of the mould, and strict process control. This includes monitoring the temperature and pressure of the molten material, as well as performing regular inspections of the finished parts.
Conclusion
Injection moulding is an incredibly efficient and cost-effective way to mass-produce parts. It’s used to produce a wide variety of products, from medical devices and consumer electronics to automotive components and industrial parts. Injection moulding is a reliable and repeatable process, capable of producing high-quality, complex parts with tight tolerances.
In this article, I’ve broken down the basics of what injection moulding is, the benefits it provides, and how it works. I hope this article has given you a better understanding of the injection moulding process, and you’re now ready to take your first steps in injection moulding!
So, what are you waiting for? Get ready to be amazed by the power of injection moulding!