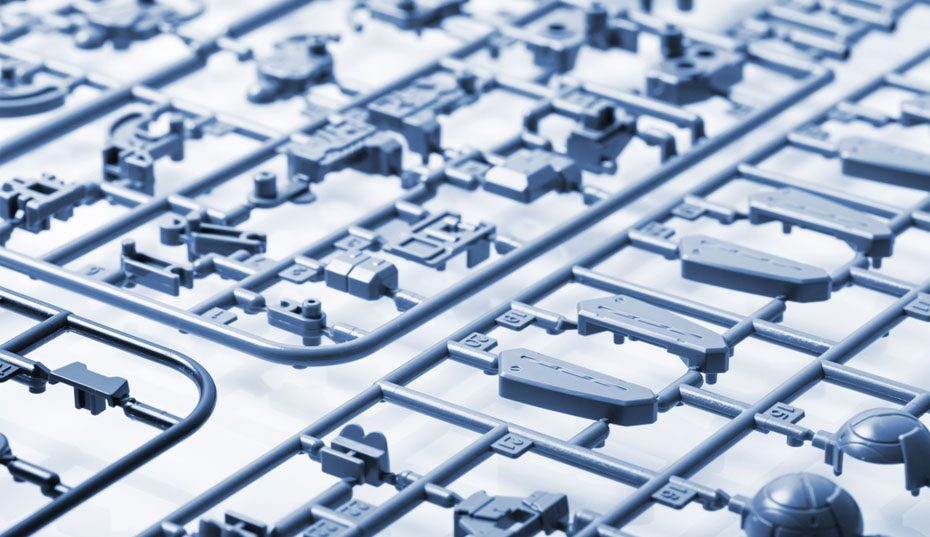
Plastic runner injection molding is a cost-effective solution for creating products with complex designs. It can be used to produce plastic parts with intricate details, allowing for a high degree of precision. Its versatility makes it suitable for a wide range of applications, including medical and automotive components.
In plastic injection molding, the plastic material is melted and injected into a mold cavity. The plastic then cools and solidifies, taking the shape of the mold. In many cases, the plastic is injected into the mold through a series of channels called runners. The runners distribute the plastic evenly to the various cavities in the mold, ensuring that all parts are the same and have consistent dimensions. The runners are typically made of the same material as the part being molded. After the parts are removed from the mold, the runners are typically trimmed off or recycled.
If you're looking for a reliable way to produce plastic components in high volume, plastic runner injection molding is the process you should be considering. This process is used to create parts that require precise dimensions and exceptional detail. In this blog post, we'll discuss the benefits of plastic runner injection molding and provide tips for choosing the right plastic runner injection molding machine, so you can be sure you'll get the best results.
What is plastic runner injection molding?
Plastic runner injection molding is a process used to create plastic components with precise dimensions and exceptional detail. It involves using a heated barrel to inject molten plastic into a mold. The mold is then cooled, and the plastic part is removed from the mold. This process is faster, more efficient, and more cost-effective than other plastic molding processes.
The plastic runner injection molding process is divided into three phases: injection, cooling, and ejection. In the injection phase, molten plastic is injected into a mold cavity. In the cooling phase, the mold is cooled and the plastic part is allowed to solidify. Finally, in the ejection phase, the plastic part is removed from the mold.
Benefits of plastic runner injection molding
There are several benefits to the plastic runner injection molding process. First, the process is fast and efficient. It is capable of producing parts with precise dimensions and exceptional detail in a fraction of the time it would take to produce the same parts using other methods.
Second, the process is cost-effective. Plastic runner injection molding is less expensive than other methods of plastic molding, making it an ideal choice for companies looking to produce parts in high volume at a lower cost.
Third, the process is flexible. Plastic runner injection molding can be used to produce parts in a wide range of sizes, shapes, and materials. This makes it an ideal choice for companies that need to produce parts in a variety of shapes and sizes.
Fourth, the process is reliable. The process produces parts with consistent quality and precise dimensions, making it a reliable choice for companies that need to produce parts with exacting specifications.
Finally, the process is environmentally friendly. The plastic runner injection molding process produces fewer emissions than other plastic molding methods, making it an ideal choice for companies that are looking to reduce their environmental impact.
Plastic runner injection molding process
The plastic runner injection molding process begins with the preparation of the mold. The mold is designed to create the desired shape and size of the part. The mold is then placed into a heated barrel, where the molten plastic is injected into the mold.
Once the plastic has been injected into the mold, the mold is cooled. The plastic part is then removed from the mold and the process is complete. The plastic part is then ready to be used in the desired application.
Tips for choosing the right plastic runner injection molding machine
When selecting a plastic runner injection molding machine, it is important to choose a machine that is capable of producing parts with the desired dimensions and detail. It is also important to consider the size and capacity of the machine. The size of the machine will determine the size of the parts that can be produced, while the capacity of the machine will determine how many parts can be produced in a given amount of time.
In addition, it is important to consider the cycle time of the machine. The cycle time is the amount of time it takes for the machine to complete one cycle of the plastic runner injection molding process. A longer cycle time will result in longer lead times for parts production, while a shorter cycle time will result in shorter lead times.
Finally, it is important to consider the cost of the machine. Different machines have different costs, so it is important to compare the cost of different machines to find the one that is best suited to your needs.
Benefits of using plastic runners in injection molding
Plastic runners are an essential part of the plastic runner injection molding process. Plastic runners are used to transport the molten plastic from the heated barrel to the mold. The runners help ensure that the plastic is evenly distributed throughout the mold and that the parts produced have consistent dimensions and detail.
In addition, plastic runners can be used to create complex and intricate shapes. The runners can be used to create intricate parts with multiple layers and intricate details, making them a great choice for companies looking to produce parts with complex shapes and details.
Advantages of plastic runner injection molding
Plastic runner injection molding offers several advantages over other methods of plastic molding. First, the process is fast and efficient, allowing companies to produce parts in high volume with minimal lead time. Second, the process is cost-effective, making it an ideal choice for companies looking to produce parts in high volume at a lower cost. Finally, the process is reliable, producing parts with consistent quality and precise dimensions.
Challenges of plastic runner injection molding
Although plastic runner injection molding offers many advantages, it is not without its challenges. One of the biggest challenges is the need to maintain the quality and consistency of the parts produced. The plastic runner injection molding process requires precise temperature control and precise timing to ensure that the parts produced have consistent dimensions and detail.
In addition, the process requires a skilled operator to ensure that the process is running smoothly and that the parts produced are of the highest quality. This requires the operator to be knowledgeable about the process and to be able to troubleshoot any problems that may arise.
Finally, it is important to be aware of the environmental impact of the process. The plastic runner injection molding process produces emissions that can be harmful to the environment if not properly managed.
Tips for reducing plastic runner waste
One of the most important aspects of the plastic runner injection molding process is reducing plastic runner waste. Plastic runner waste is created when molten plastic is not used in the production process and is instead discarded.
There are several ways to reduce plastic runner waste. First, it is important to ensure that the plastic runner injection molding machine is properly maintained. Proper maintenance will ensure that the machine is running efficiently and that the molten plastic is being used as efficiently as possible.
Second, it is important to use the right type of plastic for the application. Different types of plastics have different properties, and it is important to choose the right type of plastic for the application to ensure that the parts produced have the desired properties.
Third, it is important to use the right amount of plastic for the application. Using too much plastic will result in excess plastic that must be discarded, while using too little plastic will result in parts that are not of the desired quality.
Finally, it is important to use the right temperature for the application. Different plastics require different temperatures for optimal performance, so it is important to use the right temperature for the application to ensure that the parts produced have the desired properties.
Case studies of successful plastic runner injection molding projects
There are several case studies of successful plastic runner injection molding projects. One example is a project by a plastics manufacturer in the United States that used plastic runner injection molding to produce parts for the automotive industry. The project was successful because the parts produced had precise dimensions and exceptional detail, allowing the manufacturer to produce parts with minimal lead time and at a lower cost.
In another example, a company in Europe used plastic runner injection molding to produce parts for the medical industry. The project was successful because the parts produced had precise dimensions and exceptional detail, allowing the company to produce parts with minimal lead time and at a lower cost.
Conclusion
Plastic runner injection molding is a fast, efficient, and cost-effective process for producing plastic components with precise dimensions and exceptional detail. The process is reliable and environmentally friendly, making it an ideal choice for companies looking to reduce their environmental impact.
When choosing a plastic runner injection molding machine, it is important to consider the size and capacity of the machine, the cycle time of the machine, and the cost of the machine. It is also important to be aware of the environmental impact of the process.
Finally, it is important to use the right type of plastic for the application, use the right amount of plastic for the application, and use the right temperature for the application in order to reduce plastic runner waste.
Plastic runner injection molding offers many benefits and is an ideal choice for companies looking to produce parts in high volume with minimal lead time and at a lower cost. With the right machine and a skilled operator, companies can be sure that their plastic parts will be produced with the highest quality and precision.