When it comes to manufacturing plastic parts on a large scale, injection molding is the go-to method. A critical component of this process is the injection molding die, which plays a pivotal role in shaping the final product.
In this blog, we will explore the world of injection molding dies, specifically focusing on ACE, a renowned injection molding die manufacturer. We will delve into the top 10 tips for designing an effective injection molding die, walk you through the journey from concept to creation, and address common challenges in the manufacturing process and how to overcome them.
Top 10 Tips for Designing an Effective Injection Molding Die
Material Selection: The choice of material for your injection molding die is crucial. ACE recommends using high-quality steel, such as P20, H13, or S136, to ensure longevity and precision.
1. Optimized Cooling Channels: Effective cooling is essential to maintain consistent quality. Design cooling channels for efficient heat dissipation to prevent warping or other defects in the final product.
2. Gate Design: Proper gate design is the key to controlling flow and pressure during the injection process. Work closely with ACE engineers to determine the ideal gate type and location for your specific project.
3. Draft Angles: Incorporating draft angles into your design is essential to facilitate easy ejection of the molded part. ACE suggests a minimum draft angle of 1-2 degrees for most applications.
4. Parting Line Placement: Carefully consider the location of the parting line to ensure minimal flashing and parting line marks on the final product. ACE's expertise in die design can help you optimize this aspect.
5. Venting: Adequate venting is necessary to allow gases to escape during the molding process. Proper vent design is crucial to avoid defects like burning or gas traps. ACE has a long-standing commitment to ensuring optimal venting in their molds.
6. Tolerance Analysis: Pay meticulous attention to tolerances in your die design. ACE recommends using tight tolerances for critical dimensions while allowing for looser tolerances in less critical areas to maintain cost-effectiveness.
7. Mold Texture: The texture of the mold surface directly affects the appearance of the final product. Collaborate with ACE to determine the ideal texture for your specific application, whether it's matte, glossy, or textured.
8. Mold Maintenance: Regular maintenance is the key to prolonging the life of your injection molding die. ACE provides maintenance guidelines and services to keep your die in optimal condition.
9. Prototype and Test: Before mass production, create a prototype and conduct thorough testing to validate your design. ACE can help with prototyping and assist in making necessary adjustments.
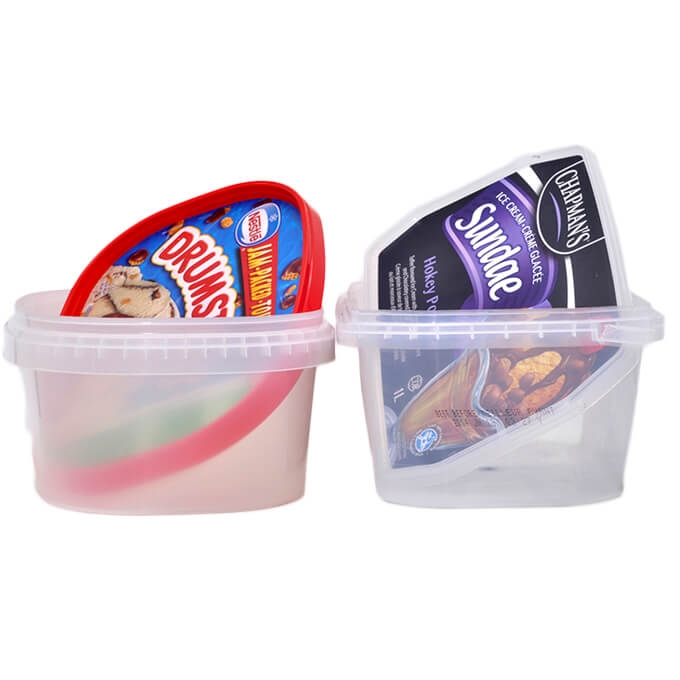
From Concept to Creation: The Injection Molding Die Manufacturing Process
The journey from an idea to a functional injection molding die is a well-coordinated process. ACE follows these key steps to ensure the highest quality dies:
1. Design and Engineering: Injection Molding Die
The process starts with meticulous design and engineering. ACE's team of experts collaborates closely with the client to understand the project requirements, material choice, and design specifications. Using advanced software and industry expertise, they craft the initial design, keeping in mind the top 10 tips mentioned earlier.
2. Prototyping: Injection Molding Die
After finalizing the design, ACE creates a prototype die to test and validate the design's functionality and efficiency. This step is critical for making any necessary adjustments before moving forward.
3. Tooling and Manufacturing: Injection Molding Die
Once the prototype is approved, ACE proceeds with manufacturing the actual injection molding die. They utilize state-of-the-art machinery and precision tools to create the die with the utmost attention to detail.
4. Quality Assurance: Injection Molding Die
At every stage of the manufacturing process, ACE conducts quality checks and inspections to ensure the die meets the desired specifications. This includes checks for proper material hardness, dimensional accuracy, and surface finish.
5. Testing and Validation: Injection Molding Die
Before handing over the die to the client, ACE conducts extensive testing and validation processes to ensure it performs flawlessly during the injection molding process. This includes verifying the cooling system's efficiency, gate functionality, and overall mold performance.
Common Challenges in Injection Molding Die Manufacturing Process and How to Overcome Them
Even with careful planning, challenges can arise during injection molding die manufacturing. ACE has a proactive approach to overcoming these challenges:
1. Warping and Shrinkage: Injection Molding Die
To combat warping and shrinkage issues, ACE engineers pay careful attention to material selection, cooling channel design, and the overall mold structure. These factors are vital in minimizing these defects.
2. Inadequate Venting: Injection Molding Die
Inadequate venting can lead to gas traps and burning. ACE ensures that the molds they produce have optimal venting, and they also advise clients on proper maintenance to prevent vent clogging.
3. Parting Line Issues: Injection Molding Die
The location of the parting line is crucial in preventing flashing and parting line marks. ACE works closely with clients to optimize parting line placement during the design phase.
4. Dimensional Variability: Injection Molding Die
Tolerances are critical in maintaining consistent product quality. ACE's precision tooling and quality control measures help minimize dimensional variability.
5. Mold Surface Defects: Injection Molding Die
To ensure a high-quality surface finish, ACE's expertise in mold texturing helps clients choose the right texture for their specific application.
Custom Injection Molding Die: Elevating Food Storage with ACE's Plastic Thin Wall Food Box Injection Moulding Container
1. Unveiling the ACE Thin Wall Food Box
Brand Name: ACE
Model Number: ACE THIN-CU
Feature: Disposable
OEM/ODM: Acceptable
Package: Standard or per request
Plastic Type: PP
2. Lightweight and Sturdy: The Perfect Combo
One of the key advantages of ACE's Thin Wall Food Box is its lightweight construction. These boxes are specifically designed to be easy to handle, making them a preferred choice for food storage, transport, and service. Their low weight ensures that food remains fresh, preventing spoilage and waste. These boxes are also suitable for meal prepping, allowing you to portion out meals and organize your food efficiently.
3. Easy to Store and Stack
Plastic thin-wall food boxes are designed to be space-efficient. They can be stacked neatly, taking up minimal storage space, and making them a practical choice for restaurants, kitchens, and food service establishments. In addition to efficient storage, these boxes are ideal for storing leftovers, and since they can be reheated in the box, they promote sustainability by reducing the need for additional containers or wraps. Labeling these containers for easy identification is a breeze, streamlining your kitchen organization.
Conclusion
ACE, as a leading injection molding die manufacturer, excels in designing, manufacturing, and troubleshooting injection molding dies. By following the top 10 design tips, adhering to a systematic manufacturing process, and addressing common challenges, ACE guarantees top-quality dies that meet the demanding requirements of the injection molding industry. Whether you're in the automotive, medical, or consumer goods industry, ACE is a trusted partner in the world of injection molding die manufacturing.