What is meant by Foaming mould?
- A form of plastic injection moulding technique known as "foaming mould" enables the manufacture of lighter and stronger items. A foam-like structure is produced by injecting gas into the molten plastic during the injection process. This can have a number of advantages, such as increased strength, decreased weight, and better thermal insulation.
- It is a special tool used to make complex and thorough tasks. It is a terrific method to give a unique touch to any project and can be used to make anything from sculptures and jewellery to wall art. Production of packaging materials, consumer items including toys and athletic goods, and automobile parts all often employ foaming moulding. Due to its capacity to create goods with a greater performance at a cheaper cost, the technique has grown in prominence in recent years.
The advantages of foaming mould:
The technology of foaming moulding for plastic injection moulding has a number of advantages. Among the key advantages are the following:
- It Reduced Weight:
Plastic parts can be made using foaming moulding to provide lightweight components. Adding gas to the molten plastic creates a foam-like structure that is lighter in weight since it has a lower density than solid plastic.
- Strengthened:
The foam-like structure produced by foaming moulding makes plastic items stronger and more rigid. As a result, products may be more durable and last longer.
- Improved Thermal Insulation:
Plastic components can improve their thermal insulation capabilities by having a foam-like structure formed by the foaming moulding process. This makes them perfect for applications that call for thermal insulation, such as materials for packaging.
- Reduced Shrinkage:
Gas can be added during the foaming moulding process to help minimize shrinkage, producing more accurate and exact components.
- Cost-effectiveness:
This moulding can lead to cost savings since it uses less material, has a faster cycle time, and produces a better product. Due to the decreased weight of the produced plastic pieces, it can also save shipping costs.
- Eco-friendly:
Foaming moulding is also environmentally friendly since it uses less material and produces less waste.
Energy Saving Potential of Foaming Mold:
Through lessened material consumption, enhanced thermal insulation, lightweight construction, and quicker cycle times, the adoption of foaming mould as a plastic injection moulding process can result in considerable energy savings. Foaming moulding can aid in decreasing greenhouse gas emissions and advancing sustainability by using less energy. Energy may be saved through foaming moulding in a number of ways:
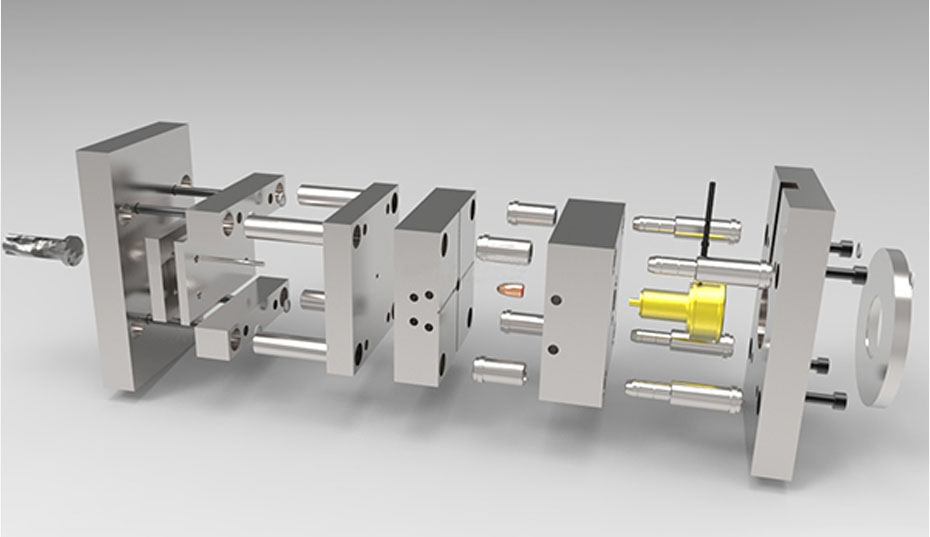
- Reduced Material Use:
By forming a foam-like structure in the plastic, foaming moulding produces a lower-density material. As a result, less raw material is needed to create the same quantity of finished goods, using less energy to extract, transport, and process the raw materials.
- Improved Thermal Insulation:
The foam-like structure produced by foaming moulding can enhance the plastic's thermal insulation capabilities, making it the perfect material for use in applications that need thermal insulation. This can result in less energy being used in applications like building insulation, where heating and cooling costs might be high.
- Lightweight Design:
Plastic components can be made via foaming moulding that is designed to be lightweight. These components may be utilized to lighten things like cars, improving fuel economy and consuming less energy as a consequence.
- Faster Cycle Times:
When compared to conventional injection moulding techniques, foaming moulding can produce faster cycle times. Because each component may be produced in less time, this can cut energy use.
What are the applications of foaming mould?
Foaming mould is an adaptable plastic injection moulding technique that may be employed in a variety of applications across many sectors. Foamed plastics are strong, lightweight materials that work well in applications where it's vital to save weight. They also work well in applications that need to regulate temperature because of their ability to insulate heat.
In many diverse applications across several sectors, foaming moulding can be employed. Foaming moulding has several typical uses, including the following:
- Industry of the Automobile:
Interior trim, door panels, and dashboard components are all frequently made using foaming moulding. Foamed plastic components are perfect for enhancing fuel economy and lowering vehicle weight since they are lightweight and robust.
- Packaging industry:
This moulding is further utilized in the packaging industry to provide insulation, cushioning protection, and foam trays for packing. Foamed plastics are the best material to use to carry goods at the desired temperature because of their thermal insulation capabilities.
- Industry of Consumer items:
A variety of consumer items, including toys, sporting goods, and furniture parts, are made using foaming moulding. Foamed plastics are perfect for situations where weight reduction is vital, including in sports equipment, because they are lightweight and robust.
- Construction industry:
This moulding is used in the construction industry to create insulating materials for various uses. Foamed plastics are perfect for building insulation because of their thermal insulating qualities, which can save heating and cooling expenses.
- Medical industry:
This moulding is used in the medical industry to create prostheses, orthopaedic implants, and other medical equipment. Foamed plastics are the best material for creating medical equipment since they are both sturdy and lightweight.
Conclusion:
Foaming mould is a useful plastic injection moulding technique that may provide producers and end users with several advantages. This item is growing more and more well-liked in the building sector. It can lower costs, save energy, and increase the effectiveness of many construction projects. The tools and knowledge required to create foam-like structures in plastic products through injection moulding are normally available from ACE, which provides foaming moulding services. In addition to offering a variety of foamed plastics with various qualities to suit various applications, we can collaborate with clients to design and build bespoke components that fit their unique specifications.