Plastic molding company: find out how to hire
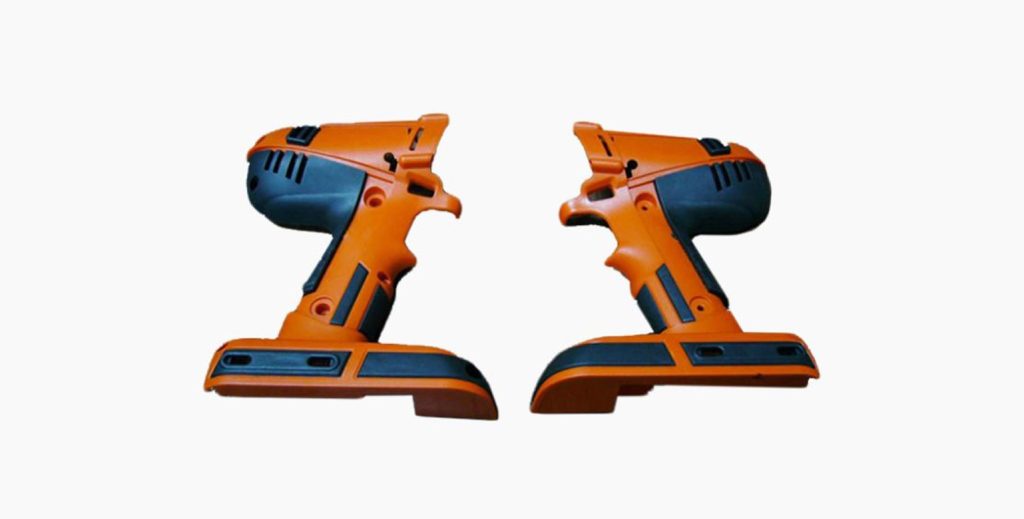
Plastic over Mold Company is ideal for those who need security and protection for electronic parts of your company. In addition to the low cost and efficiency, discover other benefits of hiring a plastic mold factory for your company now!
The manufacture of plastic injection molds has the main function of protecting and increasing the durability of electronic devices.
Generally, professional are manufacturer of plastic molds have extensive experience in the plastic boxes. Moreover, they have serving for electronics market, through differentiated technology without the use of molds or special tools.
To understand this even better, we have separated this exclusive content that will help you understand and choose the plastic molding company for your product.
What are the qualities of over Mold Company?
- What does a plastic injection mold manufacturing company do
- Furthermore, how does plastic molding work?
- What is the difference between plastic manufacturer with or without molds?
- A plastic molding company that uses the latest technology
What does a plastic injection mold manufacturing company do?
A plastic over Mold Company, as we said in the introduction, is responsible for producing plastic parts. Moreover, it provides practicality and safety for projects involving electronic parts.
That is, if you have an electronic parts factory or need to ensure more safety for your company's parts, a plastic mold company is the solution you need.
How does CNC plastic molding work?
Now you have understood the benefits of investing in the CNC machine and outsourcing the services of the injection mold maker. Now, let’s study, in a didactic way, how plastic molding works through this powerful technology.
Basically, we analyze your electronics, the amount of molds needed, the most suitable and clear material, the color you want.
We have experience to identify the best way to follow and maintain the initial design of the client's project. Therefore, the whole process must be thought and planned with caution.
Only after the project is approved will we start the manufacturing process.
After the production of the pieces, they go through some finishing stages. Here, we can carry out manually or by automatic machines, but that is the decision of the plastic molding company.
Subsequently, we emphasize that, like all manufacturing machinery, it is of paramount importance that the plastic molding company conducts its periodic inspection and review.
Therefore, before closing any deal in a plastic over mold company, our tip is to ask and see how the company deals with the revisions of its machines.
Maintain Seamless Production Plan
This ensures that the machining of flat thermoplastic sheets goes according to plan, avoiding wear, delay in production time and material loss.
That said, we brought it down simply and to make it clearer, what is the difference between these manufacturers, look!
What is the difference between plastic manufacturer with or without molds?
As we mentioned earlier, it is important to understand what actually changes when choosing the plastic factory and to identify whether or not it uses the mold manufacturing format.
Some over mold manufacturers use plastic molding before production and not the direct manufacture of cabinets and other protective parts for their electronics.
So, do you already know which is the best plastic molding company for your company?
The manufacture of metal objects by casting has been known to mankind for several millennia. All this time, the melt flowed into the mold under the influence of gravity.
Low pressure casting scheme
In the middle of the twentieth century, a new casting method appeared, the essence of which consists in feeding the melt into the mold and cooling it under low excess air pressure. Basically, the method is common for the manufacture of parts from non-ferrous metals, their alloys and plastics.
Types of injection molding
Low pressure metal casting
Low pressure casting has gained a well-deserved popularity in the non-ferrous metallurgy. Most of the parts of small, medium and large series for many industries come in this way.
Low pressure casting machine
Traditional over mold casting of non-ferrous metals and their alloys retains its position in the manufacture of jewelry, sculptures and micro-series products.
Injection molding of plastics
Plastic casting emerged almost immediately after the introduction of the metal casting method. And it became widely common. Moreover, 95% of all parts made from plastics are molded. Furthermore, several methods of plastic molding developed and widely famous:
- The most used method came by high pressure and speed of injection of material into the mold. It is famous for products with complex geometry, with thin or thick walls.
- The overpressure is not high; the initial volume of injected material is less than the volume of the mold. The material continues to expand in the form and fills it. It is good for castings of a simple shape and with low surface detail.
- Injection press. Used for products with a large surface. The pressure on the melt, in addition to the feeding force, is also produced due to the closing of the parts of the mold.
High pressure casting
The method is used in both ferrous and non-ferrous metallurgy and makes it possible to obtain the most accurate and homogeneous castings. Metal under high pressure enters the mold at a speed of up to 120 m / s. and fills out the form instantly.
High pressure casting
Generally, parts obtained by metal injection molding practically do not require finishing machining. Moreover, this method can be used to cast parts of almost any configuration, with thin walls, with finished holes and even with finished threads.
Injection molding
The injection method is different from conventional injection molding in that the metal enters the matrix as a powder mixed with a binder. The molds are made of high-strength steels. The high fluidity of the over mold mixture allows filling the smallest details of the relief of forms of the most complex configuration, including internal cavities.
Low pressure casting technology
The low pressure casting machine is a complex and deeply automated production complex with the lowest number of manual operations.
Generally, we can find it in a sealed chamber and includes:
- crucible for melting the charge;
- metal line lowered into the crucible;
- In addition, a mold with channels for supplying the melt and a gas discharge system;
- pipelines for pressurizing air or inert gas;
- Similarly, automatic temperature and pressure control.
Disadvantages of low pressure casting
Unfortunately, in addition to the advantages, the low pressure method also has a number of disadvantages:
Low pressure casting characteristics
- Low resource of a metal wire in contact with liquid metal. This prevents the method from being applied to refractory metals and their alloys.
- Moreover, complexity of flow rate control.
- Furthermore, reducing the level of the melt in the installation in the course of pouring it into molds.
- Achievement of low physical and chemical properties of the alloy due to a long stay in the crucible. Therefore, this can lead to defects in the injection molding.
- The overall complexity of setting up and using the over mold
The disadvantages of the method are more than offset by its advantages:
- Metal pouring automation.
- Low labor intensity of pouring, especially important is the automation of work in hazardous working conditions.
- Possibility to control the melt flow rate by operating with air or neutral gas pressurization. This makes it possible to increase the fillability of molds for casting thin-walled products.
- Improving the quality of castings by increasing the uniformity of the product.
- Saving metal use from 30% to 3 times. This is achieved by returning the liquid melt to the crucible.
Based on financial research, on average across the industry, investments in low-pressure casting technology return in half a year to a year.
- Design and development of any, including unique plastic products;
- Similarly, casting of plastic products on molds of any degree of complexity, both self-made and tolling;
Over mold manufacturing process
On the basis of our enterprise, it is possible not only to manufacture plastic products of any type (using our or your provided mold), but also work directly related to the over mold:
- development and manufacture of molds with the required resource
- completion and repair of molds;
- Production of molds for casting in small batches.
Within the same production site, molding of plastic products comes by out in parallel with the creation of new injection molds. In addition, you can order removable and semi-removable molds from us, as well as:
- with embedded element or with manual removal;
- compression;
- Furthermore, with automatic removal of the plastic product;
- direct pressing;
Scope of over mold application
The over mold method involves the production of castings from a liquid polymer injected under high pressure into a mold. Unlike traditional injection molding, injection molten metal can effectively compensate for volumetric and linear shrinkage. The finished products have other advantages:
- shock resistance;
- high elasticity;
- resistance to moisture and heat;
- ease of staining;
- wear resistance.
Conclusion
Injection of heated plastic into a mold is very famous in small-scale production due to its low cost and lack of complex post-processing. Plus, using this method, you can get products with a large wall thickness. Existing over mold technologies make it possible to cast molds to order in the shortest possible time. The whole process comes by automation.