In the world of foundry and metallurgy, gravity casting stands out as a process that combines simplicity with efficiency. This method, often known as permanent mold casting, utilizes gravity to fill a permanent mold with molten metal, creating parts that are durable and dimensionally consistent. This blog post explores the nuances of gravity casting mold production, shedding light on the design, creation, and operational aspects of the molds used in this process.
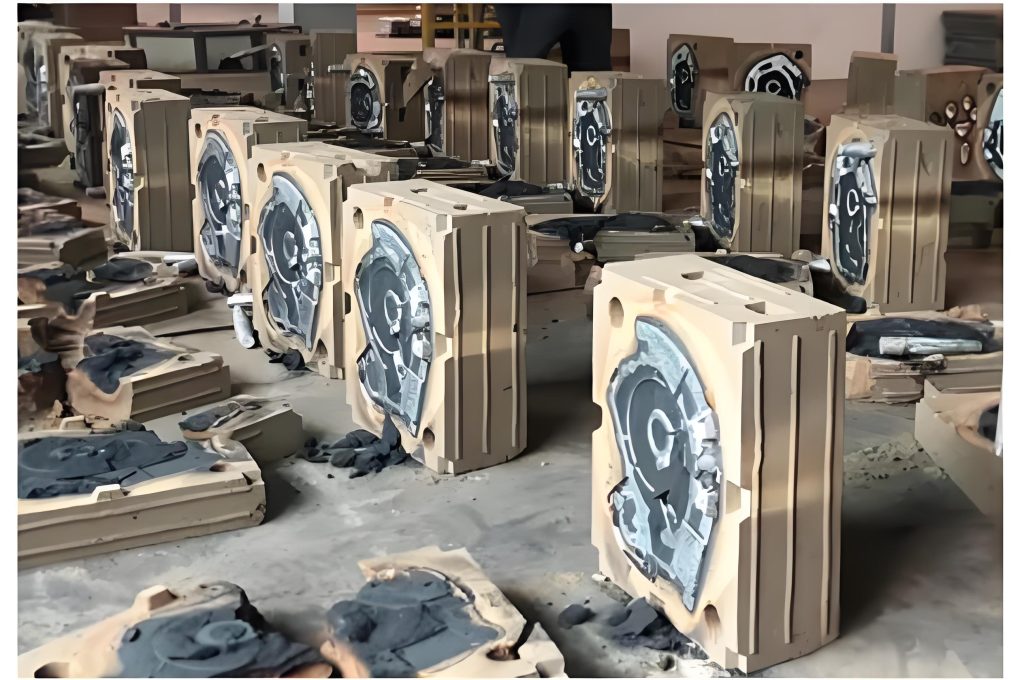
Understanding Gravity Casting
Before diving into the production of gravity casting molds, it is essential to understand what gravity casting is. Unlike other casting processes that use pressure or centrifugal force, gravity casting relies on gravity to draw molten metal into the mold cavities. This method is suitable for a wide range of metals and is often chosen for its ability to produce high-quality parts without the need for high pressure or complex machinery.
Designing Gravity Casting Molds
1. Preliminary Design
The production of a gravity casting mold starts with a precise design. Engineers must consider the final part's requirements, including its size, shape, mechanical properties, and the type of metal to be cast. Computer-aided design (CAD) software plays a crucial role in this stage, allowing for accurate and flexible modeling of the mold and the cast part.
2. Material Selection
The material chosen for the mold affects its heat conductivity, durability, and longevity. Common materials for gravity casting molds include steel, cast iron, and aluminum alloys. Each material has its own advantages; for instance, steel molds can withstand high temperatures, while aluminum molds offer excellent heat conductivity, leading to faster cooling and quicker cycle times.
The Mold Production Process
1. Machining
The creation of a gravity casting mold involves machining the designed mold from a solid block of material using high-precision tools. Computer numerical control (CNC) machining centers are typically used to ensure the mold's dimensions and surface finish meet strict tolerances.
2. Surface Treatment
Once machined, the mold's surface undergoes various treatments to enhance its properties. This may include polishing to reduce surface roughness and coating to improve mold release and extend the mold's life.
3. Mold Assembly
Gravity casting molds are often made of multiple parts, including cores that create hollow sections or intricate internal geometries. The mold assembly process ensures that all these components fit together perfectly and function as intended.
Operating the Mold
1. Mold Heating
Prior to casting, the mold is heated to a specific temperature to prevent premature solidification of the molten metal. This temperature must be carefully controlled to ensure consistent casting quality.
2. Pouring
The molten metal is poured into the mold using ladles or automated pouring systems. The design of the mold's pouring basin, runner system, and gates play a significant role in the quality of the casting, influencing factors such as metal flow and solidification.
3. Cooling and Solidification
After the metal has been poured, it begins to cool and solidify within the mold. The mold design includes cooling systems or may leverage ambient air to control the cooling rate, which is critical for the structural integrity of the cast part.
4. Ejection and Finishing
Once the metal has solidified, the part can be ejected from the mold. Subsequent finishing processes, such as trimming excess material and machining to final dimensions, are performed to complete the manufacturing process.
Challenges and Solutions in Gravity Casting Mold Production
One of the challenges in gravity casting mold production is managing heat transfer. Molds must dissipate heat efficiently to prevent defects such as hot tears or warping in the final part. This is addressed through careful design of the mold's cooling system and the selection of appropriate mold materials.
Another challenge is the mold's wear and tear over time. Proper maintenance routines, such as regular inspections and repairs, are crucial for mold longevity. Additionally, applying protective coatings can minimize wear and extend the service life of the mold.
Technological Advancements
The integration of advanced technologies, such as 3D printing, has begun to make an impact on gravity casting mold production. For example, 3D-printed cores can be used to create complex internal geometries that would be difficult or impossible to machine traditionally.
Sustainability in Mold Production
Sustainability efforts in gravity casting mold production focus on reducing waste and extending mold life. Reusable molds contribute significantly to waste reduction, and the ability to recycle metal castings at the end of their life cycle further enhances the process's sustainability.
Conclusion
Gravity casting mold production is a sophisticated process that requires meticulous design, precision machining, and thoughtful operation. As technologies advance and demand for precision parts grows, gravity casting will continue to play a vital role in manufacturing. The process's simplicity, combined with the robustness of the molds, offers a reliable and cost-effective solution for producing high-quality metal parts in a variety of industries.