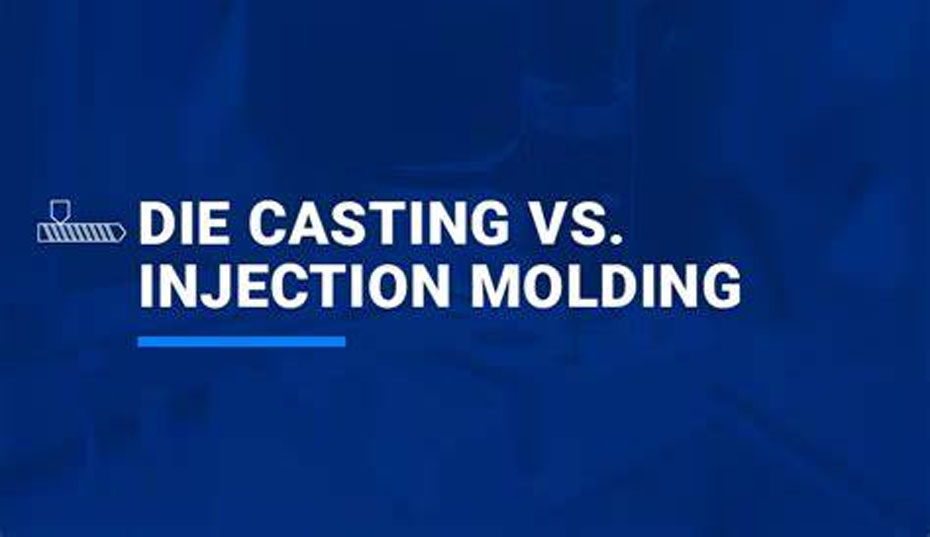
Die casting and injection moulding are two of the most common processes used in the manufacturing of metal and plastic products. They have become so popular because of their ability to produce large quantities of parts in a short time frame, and with great accuracy. But, how exactly do they work? How are they different and what are the key differences between them? In this blog article, we'll explore the key differences between die casting and injection moulding, so you can make the right decision for your product.
Introduction to Die Casting and Injection Moulding
Die casting and injection moulding are two different processes used in the manufacturing of metal and plastic products. Die casting is a metal casting process that is used to produce parts that are highly detailed, accurate, and durable. It is typically used to manufacture products like engine blocks, electrical components, and plumbing fixtures. On the other hand, injection moulding is a process that is used to produce plastic parts with a high degree of accuracy. It is used to create products like automobile parts, toys, and medical devices. Both processes have their own advantages and disadvantages, which we'll explore in this blog article.
The Process of Die Casting
Die casting is a process that involves injecting molten metal into a mould cavity under high pressure. The mould cavity is usually made from steel or aluminium and is designed to produce the desired shape and size of the product. The mould is injected with molten metal and is then cooled, allowing the metal to take the shape of the mould. The mould is then opened and the finished product is removed.
The process of die casting begins with the preparation of the mould. The mould is first filled with a wax or plastic material that will be used to create the desired shape of the product. Once the wax or plastic material has been injected into the mould, the mould is heated, allowing the wax or plastic material to melt and form the desired shape. The mould is then injected with molten metal, which will replace the wax or plastic material.
Once the molten metal has been injected into the mould, it is cooled and allowed to harden. The mould is then opened and the finished product is removed. The process of die casting is highly accurate and can produce parts with intricate details and a high degree of accuracy.
The Process of Injection Moulding
Injection moulding is a process that is used to produce plastic parts with a high degree of accuracy. It is a highly automated process that involves melting plastic pellets and then injecting them into a mould cavity. The mould cavity is designed to produce the desired shape and size of the product. The mould is then cooled, allowing the plastic to take the shape of the mould. The mould is then opened and the finished product is removed.
The process of injection moulding begins with the preparation of the mould. The mould is first filled with a wax or plastic material that will be used to create the desired shape of the product. Once the wax or plastic material has been injected into the mould, the mould is heated, allowing the wax or plastic material to melt and form the desired shape. The mould is then injected with molten plastic, which will replace the wax or plastic material.
Once the molten plastic has been injected into the mould, it is cooled and allowed to harden. The mould is then opened and the finished product is removed. The process of injection moulding is highly accurate and can produce parts with intricate details and a high degree of accuracy.
Differences in Production Speed
One of the key differences between die casting and injection moulding is the production speed. Die casting is generally faster than injection moulding, as the process is quicker and does not require as much time to cool down the metal. Die casting is also more cost-effective than injection moulding as it is faster and requires less time to produce parts.
Injection moulding is generally slower than die casting, as the process requires more time to cool down the plastic. Injection moulding is also more expensive than die casting as the process requires more time and resources to produce parts.
Differences in Durability
Another key difference between die casting and injection moulding is the durability of the parts produced. Die casting produces parts that are more durable than injection moulding as the metal is stronger and more resistant to wear and tear. The metal used in die casting also has a longer lifespan than the plastic used in injection moulding.
Injection moulding produces parts that are less durable than die casting as the plastic is less strong and more prone to wear and tear. The plastic used in injection moulding also has a shorter lifespan than the metal used in die casting.
Differences in Cost
The cost of the parts produced using die casting and injection moulding also varies. Die casting is generally more cost-effective than injection moulding as the process is faster and requires less time and resources to produce parts. Injection moulding is typically more expensive than die casting as the process requires more time and resources to produce parts.
Differences in Design Complexity
The complexity of the design of the parts produced using die casting and injection moulding also varies. Die casting is typically better suited for parts with complex designs as the process is more accurate and can produce parts with intricate details. Injection moulding is generally better suited for parts with simpler designs as the process is less accurate and cannot produce parts with as much detail.
The Benefits of Die Casting and Injection Moulding
The benefits of die casting and injection moulding are numerous. Die casting is an efficient process that produces parts with a high degree of accuracy and can be used to produce parts with intricate details. Injection moulding is also an efficient process that produces parts with a high degree of accuracy and can be used to produce parts with complex designs. Both processes are cost-effective and can be used to produce parts quickly and efficiently.
Common Applications of Die Casting and Injection Moulding
Die casting and injection moulding are commonly used to produce a variety of products, from engine blocks and electrical components to toys and medical devices. Die casting is typically used to produce products that require high accuracy and intricate details, such as engine blocks and electrical components. Injection moulding is typically used to produce products that require complex designs, such as toys and medical devices.
Conclusion
Die casting and injection moulding are two of the most common processes used in the manufacturing of metal and plastic products. They both have their own advantages and disadvantages and the key differences between them can help you make the right decision for your product. Die casting is typically faster and more cost-effective than injection moulding, while injection moulding is generally better suited for parts with complex designs. Both processes are efficient and can be used to produce parts quickly and efficiently.